
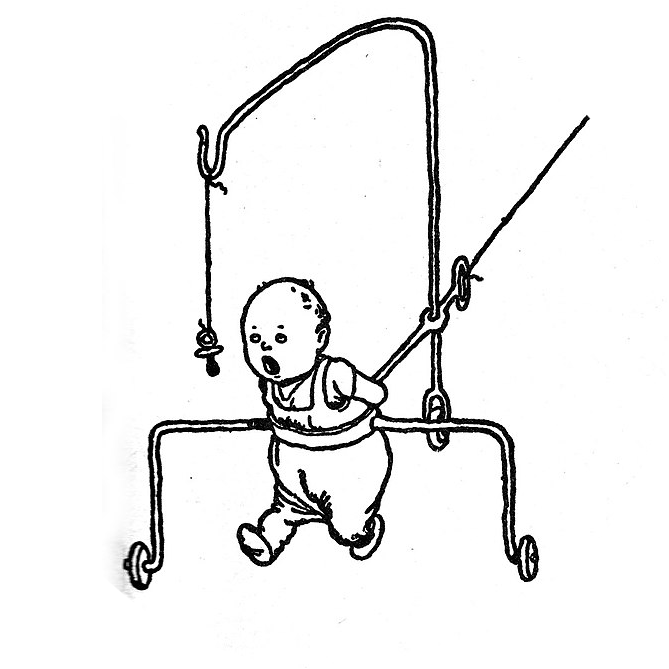
pungent oder of RTV gasket maker
Just if you’re interested: there are a tonne of different silicone chemistries.
Single part curing (no mixing needed, cure when exposed to air):
- Acetoxy (emit acetic acid)
- Alkoxy (emit methanol)
- Acetone
- Ketoxime (don’t know if this one smells)
Two-part curing (you have to mix the two components, then it starts setting):
- Condensation cure (tin catalyst) cheaper
- Addition cure (platinum catalyst) basically better in every way but more expensive
Absolutely amazing. Going to go for the offline port though, I don’t trust my save data to my browser.
N.B. Only worked in Chromium (not Firefox) for me. Could be due to addons though, not sure.